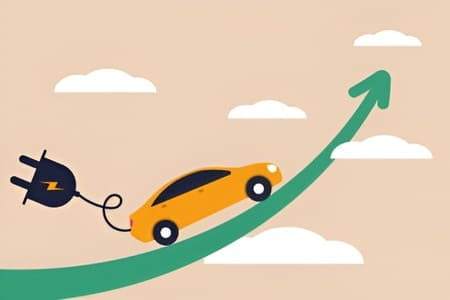
Currently, environmental regulations demand a reduction in the carbon footprint due to the high pollution rate. One of the main causes of pollutant emissions are vehicles that use fossil fuels, not only because of the mobility of these cars, but also because of the way they are manufactured.
For this reason, electric vehicles are becoming a major player in the market, and it is expected that from 2030 onwards they will be the only type of vehicle being manufactured. The aim? To achieve cities with better air quality.
For this reason, electric vehicles are becoming a major player in the market, and it is expected that from 2030 onwards they will be the only type of vehicle being manufactured. The aim? To achieve cities with better air quality.
What role does plastic play in sustainable mobility?
As demand for electric cars grows rapidly, we look for ways to optimise them as much as possible in terms of sustainability. One of the key points for improving these vehicles is autonomy, and here plastic plays a very important role.
Engineering plastics have very favourable qualities for the automotive industry. The main advantage is that they are easy to mould and create very specific parts, as well as their resistance to rust, but the most important advantage is their low weight.
Currently, the metal parts of electric cars are being replaced by thermoplastics such as polypropylene in order to reduce the weight of the vehicle and increase its autonomy. With thermoplastics, the weight of the part can be reduced by up to 60%, which means a 7% reduction in fuel consumption. Not only that, but the qualities of the plastic also guarantee the strength of the entire structure!
An even more sustainable approach
Engineering plastics have very favourable qualities for the automotive industry. The main advantage is that they are easy to mould and create very specific parts, as well as their resistance to rust, but the most important advantage is their low weight.
Currently, the metal parts of electric cars are being replaced by thermoplastics such as polypropylene in order to reduce the weight of the vehicle and increase its autonomy. With thermoplastics, the weight of the part can be reduced by up to 60%, which means a 7% reduction in fuel consumption. Not only that, but the qualities of the plastic also guarantee the strength of the entire structure!
An even more sustainable approach
Looking ahead to the future, not only is the use of plastics for electric vehicles expected to grow by more than 30%, but the use of bioplastics and recycled plastics is also increasing to further reduce vehicle weight and to make manufacturing more sustainable.