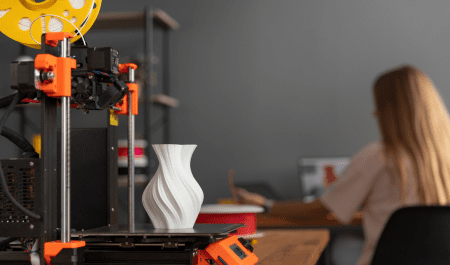
If you follow our blog, you’ve probably seen that we have a section dedicated to 3D Printing. Today we’ve prepared an infographic to summarize all the 3D printing processes we've discussed: differences between the most commonly used processes, characteristics of each, key factors… A quick guide to get a first-hand understanding of this technology!
The FDM technology is probably the most well-known. It consists of melting and depositing thermoplastic filament layer by layer. Main features:
In this process, the material is selectively melted to form strong, solid parts. Main features:
SLA works through a laser that solidifies a photosensitive liquid resin layer by layer. Main features:
This process is an evolution of FDM, using filaments reinforced with carbon, glass, or other fibers. Main features:
In this process, a laser sinters plastic powder layer by layer, creating parts without the need for supports. Main features:
Key factors: Powder grain size, laser power and precision.
This is an optimized variant of standard SLA, focused on delivering maximum detail and minimal tolerances. Main features:
The best option depends on factors such as: the final use of the part (prototype, functional, visual), the properties you are looking for (strength, detail, lightness), and your budget and production volume. At Induplast we can help you select the most suitable technology and material for your project, ensuring high-quality parts and solutions tailored to your needs.
What are the 3D Printing Methods?
3D printing has become a key resource for plastic machining and the manufacturing of customized parts. There are different technologies, each with its own advantages, limitations, and ideal applications. In this article, we explain the main differences between the most commonly used 3D printing processes in the industry so you can identify which one best fits your needs.
FDM (Fused Deposition Modeling)
The FDM technology is probably the most well-known. It consists of melting and depositing thermoplastic filament layer by layer. Main features:
- Affordable and accessible.
- Suitable for functional prototypes and simple parts.
- Acceptable mechanical properties, although resolution and surface finish are lower than other technologies.
Fusion-Based Additive Manufacturing
In this process, the material is selectively melted to form strong, solid parts. Main features:
- Excellent cohesion and density.
- Perfect for final functional parts.
- High structural stability.
Stereolithography (SLA)
SLA works through a laser that solidifies a photosensitive liquid resin layer by layer. Main features:
- Maximum precision and detail.
- Smooth surfaces and high-quality finishes.
- Ideal for visual models or molds, although parts may be fragile under demanding mechanical applications.
Fiber-Reinforced Filament Fabrication
This process is an evolution of FDM, using filaments reinforced with carbon, glass, or other fibers. Main features:
- Great stiffness and structural strength.
- Weight reduction compared to metal parts.
- Requires special nozzles due to wear from fibers.
SLS (Selective Laser Sintering)
In this process, a laser sinters plastic powder layer by layer, creating parts without the need for supports. Main features:
- Allows very complex geometries.
- Robust and functional parts.
- Rough texture that may require post-processing.
Key factors: Powder grain size, laser power and precision.
High-Precision and High-Quality SLA
This is an optimized variant of standard SLA, focused on delivering maximum detail and minimal tolerances. Main features:
- Parts with fine details and exceptional finishes.
- Ideal for visual prototypes, molds, and parts where aesthetics are critical.
- Requires additional curing and a controlled environment to maintain precision.
Which 3D Printing Technology Should You Choose?
The best option depends on factors such as: the final use of the part (prototype, functional, visual), the properties you are looking for (strength, detail, lightness), and your budget and production volume. At Induplast we can help you select the most suitable technology and material for your project, ensuring high-quality parts and solutions tailored to your needs. Want to know more or need a custom part? Contact our technical team and discover how we can help turn your idea into a real, functional part!