At Induplast we are specialists in machining engineering parts.
When we receive technical engineering enquiries on machining processes, we need to know all the details of the project in order to give our customer the best advice on the material to use and, wherever possible, we opt for polymers (engineering plastics) as the best alternative.
Especially in those applications in which a good weight/mechanical strength ratio is required.
Compared with other materials, engineering plastics offer many advantages, such as their versatility (they are used in all industrial areas), their elasticity (when heated, their shape can easily be changed), they are inert, lighter, durable, provide electrical insulation and absorb impact energy.
They are highly resistant to corrosion and chemical attack, and have better noise and vibration absorption.
They are also more cost-effective, as are the processes in which they are used.
At an environmental level, they are notable for energy and fuel saving in their production and transport due to their light weight and possibility of recycling (thermoplastics can be recycled as many as 5 to 6 times without altering their original properties).
The polymer takes shape after forming and machining processes.
The first provides practically finished parts, and machining takes away excess material by stock removal or abrasion to end up with the defined shape of the designed part, or the part assemblies are put together to form a final larger object.
The machining is carried out on a semi-finished workpiece, starting from a plastic plate or rod.
It is important to know that all engineering plastics can be machined, and that, depending on the application, the polymer to be used and the machining process is decided according to requirement.
Machining is a set of different processes, notable among which are:
Turning: This is done on a lathe that rotates the workpiece about its axis of revolution.
The workpieces can be turned both internally and externally.
Circular slots can be created in the workpiece, it can be given a conical or cylindrical shape, through holes can be created, and threads can be produced to form the workpiece into a bolt.
Milling: This combines the rotary movement of a cylindrical tool, with cutting teeth around its periphery called the milling cutter, with the linear movement of the workpiece in order to generate flat surfaces. The milling cutter is used to make slots, cuts, stock removal in circular, helical, gear etc. forms.
Drilling: The combination of the rotation movement plus the advance of a specific tool known as a bit creates cylindrical holes.
With some plastic materials, their low thermal conductivity and high expansion due to heat has to be taken into account, and special care must be taken to lift the bit frequently and facilitate the cooling of the workpiece.
If large holes need to be machined, first we advise starting with a medium bit or making a cavity first. In the same way, the drilling process must be progressive with the continuous removal of swarf.
Sawing: This consists of opening slots in the material to separate it into parts, small workpieces or sections of round bar are cut with angles and exact dimensions with the help of numerical control machines.
Brushing: this process removes the stock from flat workpieces to reduce their thickness, by cutting with a cutting blade inserted in the tool.
Finishing: removing small quantities of stock that allows very accurate dimensions to be achieved, as well as very good surface finishes.
Shearing: cutting that rips the sheet by means of the action of two blades that slide over one another, without being able to make a curved cut.
Cutting with wire: The machining of expanded or extruded polystyrenes is carried out by cutting the excess material using a hot wire.
As specialists in machining processes, we have complete machinery centres in our workshops: automatic and manual CNC lathes, milling machines, saws, drills, automatic threading machine, brushes, auxiliary machinery.
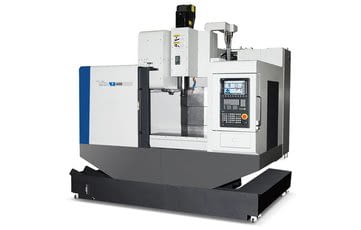
And, lastly, some advice to take into consideration to avoid problems throughout the plastic workpiece machining process:
- High machining speeds must be used to prevent tearing, and depending on the polymer.
- Temperatures must be controlled, as some thermoset plastics can breakdown at excessive temperatures and there are thermoplastics that can become deformed.
- During the stock removal operation, excess material must be prevented from adhering to the final part. Powerful coolants must be used – compressed air jet or emulsion for drilling.
- Cutting tools for working the plastics must be heat- and wear-resistant.
If you have any technical queries on particular technical aspects of any of the processes described above, don't hesitate to ask us.