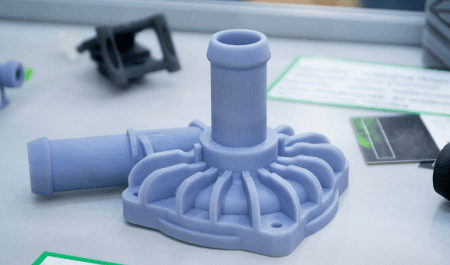
In the world of additive manufacturing, SLS (Selective Laser Sintering) technology has become one of the most powerful and versatile methods for plastic machining. With its ability to produce complex and durable parts, SLS is revolutionizing the way we create prototypes and final products.
In this article, we’ll take a deep dive into this fascinating technology and its applications!
SLS technology offers a unique combination of design freedom, strength, and versatility. As the technology continues to evolve, we can expect to see even more innovative applications across industries. Are you passionate about the world of 3D technology? Discover the most popular 3D printing methods in our blog!
You might also be interested in...
FDM Technology or Fused Deposition Modeling (1)
In this article, we’ll take a deep dive into this fascinating technology and its applications!
What is SLS in 3D Printing?
SLS is a 3D printing process that uses a high-powered laser to fuse polymer powder particles layer by layer, creating three-dimensional objects. Unlike other technologies, SLS does not require support structures, as the unsintered powder itself acts as support during printing.
How Does SLS Work in 3D Printing?
- Powder Preparation: A polymer powder bed is loaded into the SLS machine.
- Laser Sintering: A computer-controlled laser traces the outline of each layer in the powder bed, fusing the particles.
- Lowering the Powder Bed: The bed lowers one layer, and a new layer of powder is applied.
- Process Repetition: Steps 2 and 3 are repeated until the part is completed.
- Part Retrieval: The part is removed from the powder bed and cleaned.
Advantages of SLS
- Design Freedom: Enables the creation of complex geometries and interlocking parts.
- High Strength and Durability: SLS parts are strong and functional, suitable for demanding applications.
- Material Versatility: Compatible with a wide range of polymers such as nylon, TPU, and more.
- Small Batch Production: Ideal for prototyping and short-run manufacturing.
- No Support Structures Needed: Reduces post-processing time and material waste.
Applications in Plastic Machining:
- Functional Prototypes: Allows testing and validation of designs before mass production.
- Customized Parts: Ideal for creating unique or tailored components for specific needs.
- Tools and Fixtures: Enables the production of customized tools and jigs for manufacturing.
- End-Use Industrial Parts: SLS parts are strong enough for demanding industrial applications.
- Medical Applications: Used in the creation of custom prosthetics and medical devices.
Common Materials Used in SLS:
-
Nylon (PA 11, PA 12): Highly popular due to its strength and durability.
- Thermoplastic Polyurethane (TPU): Flexible and abrasion-resistant.
SLS Technology Is a Powerful Tool for Plastic Machining
SLS technology offers a unique combination of design freedom, strength, and versatility. As the technology continues to evolve, we can expect to see even more innovative applications across industries. Are you passionate about the world of 3D technology? Discover the most popular 3D printing methods in our blog!You might also be interested in...
FDM Technology or Fused Deposition Modeling (1)