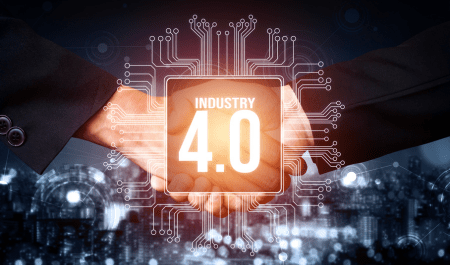
La Industry 4.0, also known as the fourth industrial revolution, is radically transforming the way we manufacture products. The integration of digital technologies such as the Internet of Things (IoT), Artificial Intelligence (AI), and BIG DATA is optimizing production processes, making them more efficient, flexible, and sustainable. In this article, we explore how Industry 4.0 is revolutionizing plastic machining, a key sector in modern manufacturing. Let’s dive in!
The integration of Industry 4.0 in plastic machining is delivering significant benefits:
Enables the connection of machines and devices, facilitating data collection and exchange.
Allows for the analysis of large data volumes and the automation of complex tasks.
Enables real-time data collection and analysis, providing valuable insights for decision-making.
Allows for the rapid and cost-effective creation of prototypes and customized parts.
Integrate the physical and digital worlds, enabling remote monitoring and control of production processes.
Industry 4.0 is transforming plastic machining—making it more efficient, flexible, and sustainable. Companies that embrace these technologies will be better equipped to compete in an increasingly demanding market. At Induplast, we are embracing new trends and applying cutting-edge technologies to stay ahead and deliver the best service to our clients.
What is Industry 4.0?
Industry 4.0 is based on the digitalization and interconnection of production processes. This includes real-time data collection and analysis, task automation, and the creation of intelligent and adaptable production systems.
Impact of Industry 4.0 on Plastic Machining
The integration of Industry 4.0 in plastic machining is delivering significant benefits:
- Increased efficiency: Task automation and process optimization reduce production time and costs. Data analysis enables real-time issue detection and correction, minimizing errors and waste.
- Greater flexibility: Additive manufacturing (3D printing) allows for fast and cost-effective prototyping and custom part production. Flexible systems easily adapt to demand shifts and small-batch production.
- Improved sustainability: Process optimization reduces energy and material consumption. The use of recycled and biodegradable materials supports the circular economy.
- Enhanced quality control: The integration of sensors and machine vision systems enables continuous product quality monitoring. Data analysis helps predict and prevent defects, ensuring consistency and reliability.
- Predictive maintenance: Sensors embedded in machinery collect performance and condition data. Analyzing this data allows for maintenance to be scheduled before breakdowns occur, preventing unexpected and costly downtime.