In the previous post, we saw that Nylon® is present in everything that surrounds us. It is an important element in our engineering part manufacturing projects for industrial machinery, thanks to its versatility and its technical properties..
Today I am going to talk about other versions of this polyamide that, although not so well known, are also present in the industrial environment and are necessary in our machining processes, including 3D additive printing. They are used in a variety of industries, but most widely for packaging and coatings (apart from the textile sector) in the automotive, mechanical engineering, etc. sectors.
Their mechanical characteristics are modified with the help of additives, fillers and stiffeners that help to adapt the polyamides to the specific requirements of each application.
Their mechanical characteristics are modified with the help of additives, fillers and stiffeners that help to adapt the polyamides to the specific requirements of each application.
Modifying the chemical structure of Nylon® can improve its stiffness and mechanical, thermal and impact resistance. Its malleability is optimised, its water absorption is lowered (they are highly crystalline polyamides, ensuring greater stability in damp environments).
We see that polyamide Nylon® PA6, PA66 has a high molecular weight, which ensures its performance in critical applications in machining processes, due to its extreme durability and strength.
Similarly, by synthesising other polyamides (PA 610, PA11, PA12 etc.), derivatives have been attained with high molecular weight that are suitable for injection and extrusion of engineering parts.
Similarly, by synthesising other polyamides (PA 610, PA11, PA12 etc.), derivatives have been attained with high molecular weight that are suitable for injection and extrusion of engineering parts.
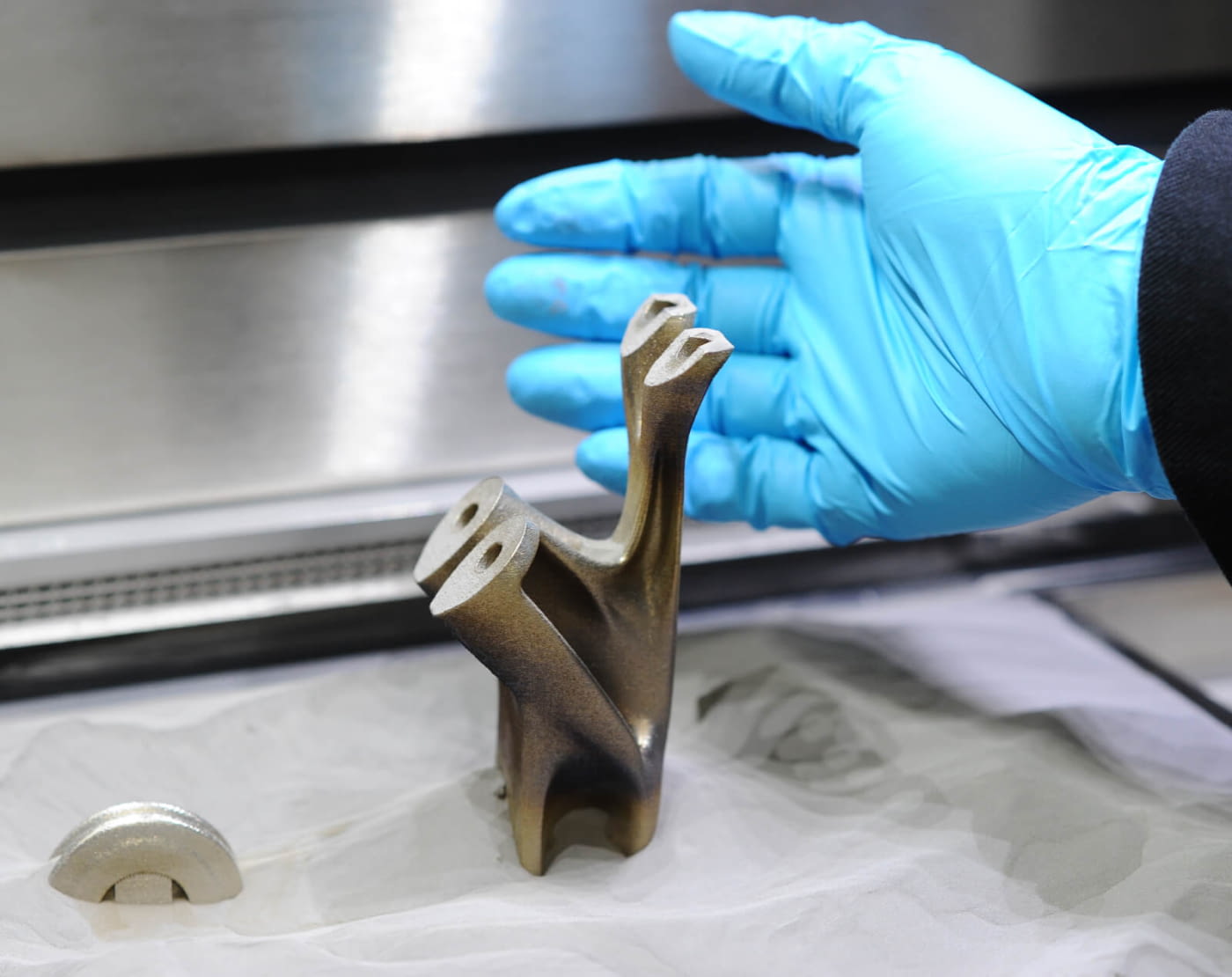
PA6(Nylon®) polyamide filaments have great flexibility, impact and abrasion resistance, and their mechanical properties are very close to that of ABS. They are a good alternative to polycarbonate because they are easy to print and ensure a longer useful life, therefore they are ideal for the printing of parts that require resistance over time: tools, hinges, machine components that require good resistance.
As a polyamide in the form of powder, PA11 and PA12 offer very high mechanical and thermal properties and resistance to chemical products.
Here is a brief summary of the most notable characteristics and industrial applications of the three polyamides mentioned in this post:
The polyamide PA11 is one of the most versatile materials, with good properties and resistance to mechanical stress, even at low temperatures, and bears impact and wear well. Reinforcing with fibre, rubber or mineral fillers considerably increases its physical-mechanical and thermal properties, underlined in its use in mechanical engineering for moving components, e.g. gears and bearings.
In 3D additive manufacturing, PA11 is typically used for mechanically loaded functional prototypes and mass-produced parts with long-lasting moving elements, such as hinges.
Another of the important applications of this material is found in the automotive industry: seals, housings, gears, flexible teeth in machinery.
The polyamide PA6.10 has good mechanical properties, heat and chemical agent resistance, low water absorption and great flexibility.
It is a good solution for applications that require high mechanical performance for traction and for continuous or alternate bending, such as robotics, pneumatics, tools and industrial machinery. Very common in the automotive sector.
The polyamide PA12 particularly features in industry 4.0, in 3D printing.
It is used in selective laser sintering, since, in contrast to filament, it absorbs little moisture and is easier to process after printing. The result is very functional parts, as the material is strong, flexible and slightly porous.
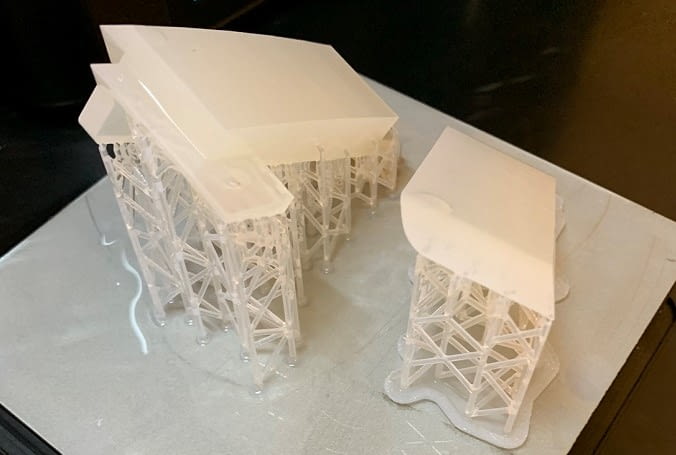
Finally, as I’m used to doing now, here is an interesting fact:
Despite their extensive use in nearly all industries and in nearly all forms of manufacture, the majority of polyamides offer a high degree of recycling.
They are repurposed into our most common garments in the textile industry.
They are also being used in the automotive industry; for example, PEUGEOT is helping to reduce harmful gas emissions by using recycled polyamides in the manufacture of their components.