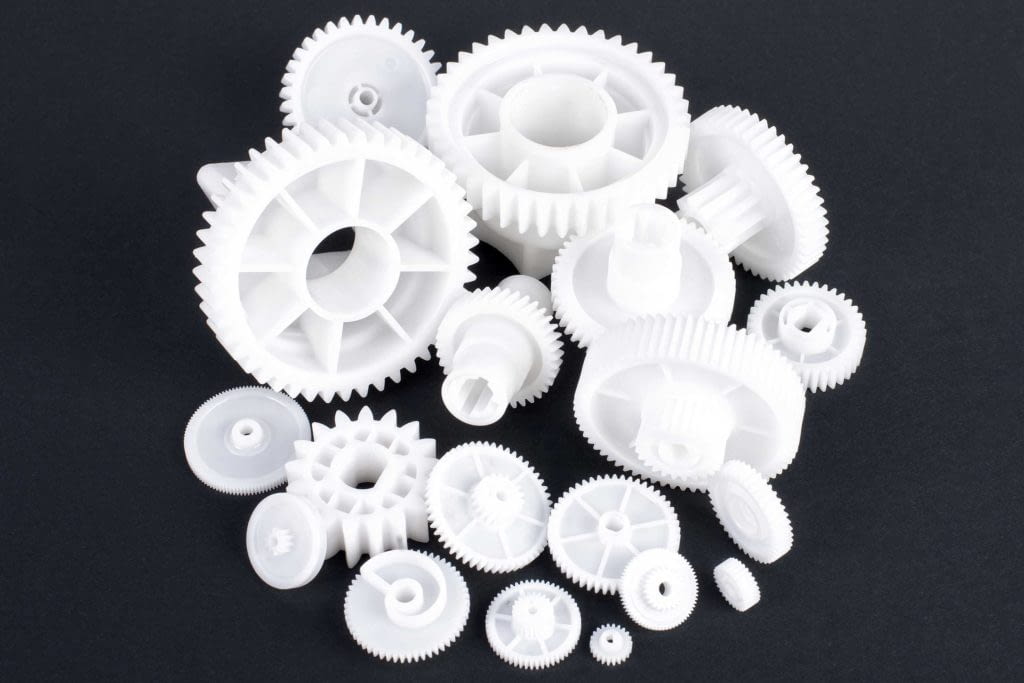
We can define a gear as a tool that allows the transmission of movement between two shafts.
Clearly, there are many types of gears, according to the size of the teeth, the ratio between the shafts and their form, among many other characteristics.
However, it is not always so simple when it comes to joining two gears, as several problems arise.
For example, the friction that can be generated between one set of gear teeth and another can give rise to temperatures that can scorch the whole system.
We can also encounter a situation where, after a long operating period, a small displacement of the gears has occurred, which could lead to a breakage of the part or even the entire machine.
To avoid this problem, the shape of the gear teeth must be carefully designed.
This is where the "Law of Gearing" concept comes in, the purpose of which is to ensure continuous uniform rotation of both gears. Download LAW OF GEARING for free.
Clearly, there are many types of gears, according to the size of the teeth, the ratio between the shafts and their form, among many other characteristics.
However, it is not always so simple when it comes to joining two gears, as several problems arise.
For example, the friction that can be generated between one set of gear teeth and another can give rise to temperatures that can scorch the whole system.
We can also encounter a situation where, after a long operating period, a small displacement of the gears has occurred, which could lead to a breakage of the part or even the entire machine.
To avoid this problem, the shape of the gear teeth must be carefully designed.
This is where the "Law of Gearing" concept comes in, the purpose of which is to ensure continuous uniform rotation of both gears. Download LAW OF GEARING for free.
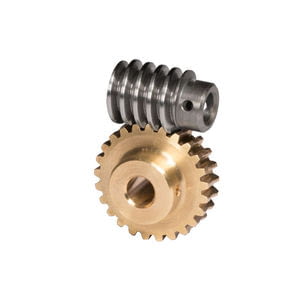
The materials used to manufacture the gears can be metal or plastic.
Plastics are very common in the mechanical industry, and in the case of geared transmission, they are used for the manufacture of the toothed wheels.
Their low cost, low inertia, low weight, noise reduction and resistance to powers of around 50 kW are some of the advantages that mechanical engineers take into consideration when deciding on the gear material, depending on its application.
Another advantage is that they can be combined with internal lubricants such as PTFE or silicone, and are usually resistant to many corrosive environments.
Plastic gears are manufactured in three ways:
- in injection moulds
- by machining processes
- by 3D printing
Those that are manufactured by injection moulding are usually very small, as the plastics usually contract as they cool, they usually have a smaller and harder surface, and there is the possibility of reinforcing them with glass fibre and adding anti-friction additives.
Gears manufactured using a machining process can be larger.
And with 3D printing, production times are much shorter, but you have to know how much force the gear is going to exert, and then decide on the manufacturing material – and the 3D printer does not work with a large variety of them.
*We recommend that the toothed wheels of the same gear intended for significant load and rotation forces are produced in different plastic materials to prevent wear damage produced by friction, which can even lead to breakage.

Engineering plastics (polymers) used in the manufacture of gears are grouped together in two main groups, which are thermoplastics and thermosets.
Some examples of the engineering plastics most used in the manufacture of gears are:
Some examples of the engineering plastics most used in the manufacture of gears are:
• PA6. Universal gear material for machine engineering; it is wear resistant and absorbs impacts, but is not recommended for small gears with high dimensional requirements.
• PA12. Hard polyamide with relatively low water absorption, therefore, higher dimensional stability than other polyamides.
We recommend it for use in areas with impact load peaks. Excellent wear resistance.
• POM-C. Due to its low moisture absorption, it is especially suitable for small gears with high dimensional stability demands.It is not recommended in dry operating applications due to its hardness, unless it can be continuously lubricated.
• PA12. Hard polyamide with relatively low water absorption, therefore, higher dimensional stability than other polyamides.
We recommend it for use in areas with impact load peaks. Excellent wear resistance.
• POM-C. Due to its low moisture absorption, it is especially suitable for small gears with high dimensional stability demands.It is not recommended in dry operating applications due to its hardness, unless it can be continuously lubricated.
The additives help to achieve an appropriate balance of mechanical, self-lubricating, wear-resistant and operating temperature properties.
• Polytetrafluoroethylene (PTFE)
• Perfluoropolyether (PFPE)
• Silicone
It is clear that, depending on the application, both plastic and metals can be good allies depending on the characteristics required.
Gears of various types, sizes and materials are widely used in various machines and systems that require a positive and step transmission.
It is important to remember that the formulas that are applied in engineering projects are not the same for the two types of material. The enormous differences in mechanical properties, the manufacturing process and the gear geometry must be assessed.
In this regard, plastic gears have greater flexibility, as regards shape and modifications.
• Polytetrafluoroethylene (PTFE)
• Perfluoropolyether (PFPE)
• Silicone
It is clear that, depending on the application, both plastic and metals can be good allies depending on the characteristics required.
Gears of various types, sizes and materials are widely used in various machines and systems that require a positive and step transmission.
It is important to remember that the formulas that are applied in engineering projects are not the same for the two types of material. The enormous differences in mechanical properties, the manufacturing process and the gear geometry must be assessed.
In this regard, plastic gears have greater flexibility, as regards shape and modifications.