- PRODUCTS
- 3D PRINTING
3D PRINTING
The manufacture of parts with 3D printers is an innovative and highly versatile technique that has led to great advances in many sectors. The reliability of this new industrial solution is gaining strength by leaps and bounds, replacing traditional machinery in a wide variety of jobs. The HP JET FUSION 3D Printer is now the key tool for the success of projects in all industrial sectors, guaranteeing high performance, precision, flexibility and optimised workflows.
Company specialised in 3D printing
Induplast stands out for its innovative nature, both in the machinery used for the manufacture of all types of parts and in the technical advice provided by our professionals. For this reason, we are committed to cutting-edge technology, placing our full trust in the HP Jet Fusion 3D printer and its multiple applications. As pioneers in the printing of 3D parts, we produce prototypes of highly complex geometries, as well as final parts in short and medium series. With the printing of 3D parts, we not only obtain finishes that exceed the strictest quality controls, but we also reduce manufacturing times in a surprising way, helping to improve profitability. Our workshops work with certified, high quality materials. In this case, the versatility of the material used for printing (polyamide-PA12) means that there are many sectors where its production fits in, such as the aeronautical, biotechnological, automotive or electrical sectors, among many others.
Custom budget for your 3D printing
Due to the variety of work that can be carried out with this type of machinery is very wide, we prepare a customised 3D printing quote for each customer. Our experts are available to advise you and help you to optimise your production. In addition to specialising in the manufacture of parts for industrial purposes, we are also involved in the design of these parts to ensure high precision and optimum process performance. Contact us for more information.
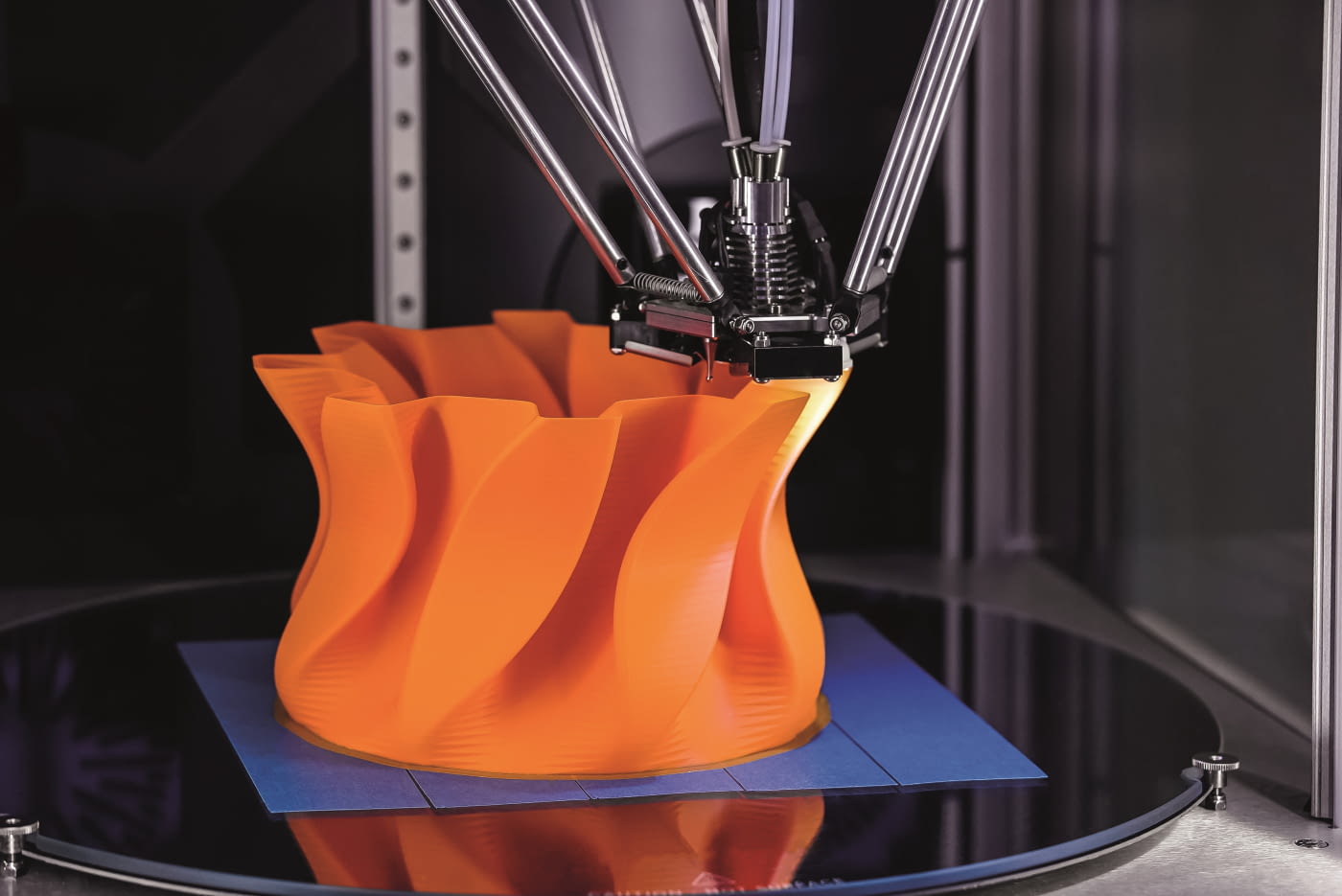
Additive manufacturing, as a modern alternative to traditional machining processes for technical parts.